CAPEX of Chemical Recycling
- APChemi Business Development
- Aug 10, 2024
- 6 min read
Updated: Aug 29, 2024
In the pursuit of a circular economy, Chemical or Advanced Recycling has emerged as a promising solution to transform plastic waste management. However, the question of capital expenditure (CAPEX) looms large. Let's explore what the CAPEX of chemical recycling should be, considering the entire value chain and the complexities of this emerging industry.

1. The Value Chain of Chemical Recycling

To understand the CAPEX of chemical recycling, we must first grasp its intricate value chain:
1. Plastic segregation from garbage: The crucial first step in giving waste a new life.
2. Pyrolysis: The heart of chemical recycling, where heat transforms plastic into valuable hydrocarbons.
3. Pyrolysis oil purification: Refining the raw output into a high-quality feedstock.
4. Conversion of purified pyrolysis oil into monomers and polymers: The final step, bringing us full circle.
Each link in this chain demands investment and contributes to the overall CAPEX picture.

2. Key CAPEX Components and Estimates

When we dissect the CAPEX of chemical recycling, several critical components emerge:
- Processing technology: Pyrolysis reactors, distillation columns, and catalytic systems.
- Feedstock preparation systems: Ensuring plastic waste is primed for transformation.
- Product handling and storage: Safeguarding valuable outputs.
- Site development and construction: The physical foundation of the operation.
- Auxiliary systems: Wastewater treatment, emissions control, etc.
- Engineering and project management: Guiding the project from concept to reality.

Recent research analysis provide some concrete CAPEX estimates:
- Advanced recycling technologies typically require USD 3,500 to over USD 7,500 per metric ton of annual capacity.
- A 40,000 ton/year mixed plastic waste pyrolysis plant is estimated to cost €20.1 million to €26.1 million.
- Small-scale molecular recycling units (average 6,300 metric tons/year) have an average CAPEX of USD 11.1 million.
- Larger-scale conversion technologies (average 150,000 metric tons/year) have an average CAPEX of USD 275 million.
3. Technical Specifications of Pyrolysis
Pyrolysis, a key technology in chemical recycling, operates under specific conditions:
- Temperature range: Typically between 300°C and 900°C, depending on the plastic type and desired products.
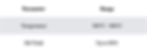
- Atmosphere: Conducted in the absence of oxygen to prevent combustion.
- Reactor types: Include fixed bed, fluidized bed, and rotary kiln reactors.
- Feedstock: Can handle various plastics, including polyethylene, polypropylene, polystyrene, and mixed plastic waste.
- Products: Main outputs include pyrolysis oil (similar to crude oil), syngas, and char.
- Product yield: Can reach up to 80% for oil production from certain plastics.
4. Balancing CAPEX Across the Value Chain
The crux of the matter is that CAPEX in chemical recycling isn't about minimizing costs at each step, but optimizing the entire system. A holistic approach is paramount. We must allocate costs judiciously across each stage, recognizing that an investment upstream might yield significant savings downstream.
The "six-tenths rule" in chemical engineering suggests that as capacity doubles, costs typically increase by a factor of about 1.52. This economy of scale principle is crucial when considering the optimal size for chemical recycling facilities.
5. Environmental Impact and Lifecycle Analysis

When evaluating chemical recycling, it's essential to consider its environmental impact compared to other recycling methods:
- A study by Sphera for BASF found that chemical recycling (pyrolysis) of mixed plastic waste emits 50% less CO2 than incineration.
- However, lifecycle analyses generally show that mechanical recycling has lower environmental impacts than chemical recycling currently.
- Chemical recycling can reduce greenhouse gas emissions by at least 50% (in 2023) and 60% (projected for 2030) compared to alternatives like incineration.
The environmental benefits of chemical recycling are projected to increase as the technology and supporting infrastructure improve.
6. Catalytic Systems in Advanced Recycling
Catalytic systems play a crucial role in improving the efficiency and selectivity of chemical recycling processes:
- Zeolites: Microporous materials, especially when containing metal nanoparticles, have shown promise for breaking down various plastic polymers.
- Metal oxides: Catalysts like ZSM-5, Y-zeolite, FCC, and MCM-41 are used to improve process efficiency and product selectivity.
- Supported metals: Ruthenium-based catalysts have been effective for hydrogenolysis of polyolefins.
- Binuclear complexes: A recently developed binuclear zinc complex has shown high activity for depolymerizing PET and other polyesters.
These catalytic systems can lower energy requirements, improve selectivity for desired products, and handle mixed plastic waste streams more effectively.
7. Regulatory Framework and Government Incentives
The regulatory landscape for chemical recycling is evolving, with significant implications for CAPEX decisions:
- The EU is implementing regulations focused on reducing plastic packaging use, improving waste handling, and increasing recycled content in plastics.
- In the US, 24 states have passed legislation exempting chemical recycling from solid waste regulations and classifying it as manufacturing.
- The U.S. Department of Energy is offering USD 750 million in grants through the Advanced Energy Manufacturing and Recycling Grant Program.
- Some governments are encouraging financial institutions to provide loans and credit facilities to recyclers.
These regulatory changes and incentives can significantly impact the economic viability of chemical recycling projects and should be factored into CAPEX calculations.
8. Market Volatility and Economic Considerations
The recycled plastics market is subject to significant volatility, which impacts CAPEX decisions:
- Recycled plastics prices have experienced dramatic fluctuations. For example, bale prices for PET, natural HDPE, color HDPE, and PP dropped by 55%, 69%, 65%, and 51% respectively in just three months.
- When the price difference between recycled and virgin plastics exceeds 20-30%, buyers tend to switch to virgin materials.
- This volatility affects the economic viability of recycling operations and can lead to the landfilling of recyclable materials due to unfavorable economics.
CAPEX models for chemical recycling must account for this volatility and include strategies to mitigate its impact, such as long-term contracts or diversified product portfolios.
9. Scaling Challenges and Solutions

As chemical recycling technologies move from pilot to commercial scale, several challenges emerge:
- Ensuring consistent quality and supply of plastic waste feedstock is challenging.
- Improving process yields and energy efficiency at larger scales is needed.
- Building out collection, sorting, and preprocessing infrastructure to supply chemical recycling plants at scale.
- Addressing public concerns about potential environmental/health impacts of large-scale facilities.
To overcome these challenges, companies are investing in:
- Advanced sorting technologies to improve feedstock quality.
- R&D to enhance process efficiency and reduce energy consumption.
- Partnerships across the value chain to secure feedstock supply and product offtake.
- Comprehensive environmental impact assessments and community engagement programs.
10. Case Studies and Industry Projections

While full-scale commercial case studies are limited due to the industry's early stage, some examples illustrate current progress:
- APChemi's technology and plant is certified for ISCC Plus. This asset is supplying purified pyrolysis oil for production of advanced recycled plastics. [Click to know more]
- APChemi's pyrolysis oil purification facility is accelerating advanced recycling by upto 12,000Kg/year of single use plastic waste. [Click to know more]
- ExxonMobil's advanced recycling facility in Baytown, Texas has the capacity to process £ 80 million (about 36,000 metric tons) of plastic waste per year.
- Neste, Borealis, Uponor, and Wastewise Group have collaborated to transform post-industrial waste plastic into high-quality pipes for the construction sector.
Looking ahead, industry projections suggest significant growth:
- Chemical recycling could produce 3.4 Mt of recycled plastics in Europe by 2030.
- European plastics manufacturers plan to increase investment in chemical recycling from €2.6 billion in 2025 to €8 billion in 2030.
- The US is expected to lead in advanced plastic recycling plants by 2025, with an estimated 140 plants globally.
11. Conclusion: The Path Forward
So, what should be the CAPEX of chemical recycling? The answer is nuanced and must be:
- Comprehensive: Covering the entire value chain
- Balanced: Distributing investment where it yields the greatest overall benefit
- Sustainable: Allowing for profitability without relying on external support
- Flexible: Able to adapt to technological and market changes
- Forward-thinking: Incorporating future revenue streams and benefits
As we stand on the brink of a recycling revolution, our approach to CAPEX will determine whether chemical recycling fulfills its promise or remains a tantalizing possibility. By embracing a holistic, value-chain approach and considering the factors discussed – from technical specifications to market volatility, from regulatory frameworks to scaling challenges – we can build a CAPEX model that not only makes chemical recycling possible but propels it to its full potential.
The future of plastic is circular. With the right CAPEX strategy, informed by comprehensive data and adaptable to an evolving landscape, we can make that future a reality.
We at APChemi, are actively engaging with stakeholders to accelerate decarbonization and circularity. Contact Us.
Subscribe our newsletter for more updates.
